Casting sandblasting machines use a variety of parts that play critical roles during the sandblasting process.
The main types of these parts include
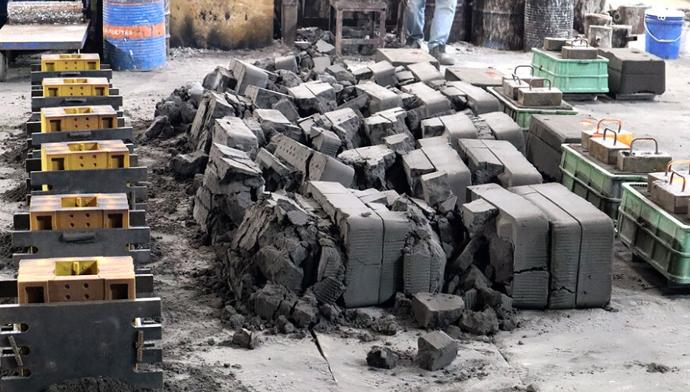
1. Nozzles
- Nozzles are the core components of sandblasting machines, responsible for spraying abrasive materials at high speed onto the workpiece surface. These nozzles must have extremely high wear resistance to withstand continuous abrasive impact. Common materials include boron carbide, tungsten carbide, and alumina ceramics.
2. Separators
- Separators are used to separate recovered abrasives and dust, ensuring the quality and recovery efficiency of the abrasives. The internal blades and liners of separators need to have excellent wear resistance and are typically made of high chromium cast iron or hardened steel.
3. Abrasive Valves
- These valves control the flow and pressure of the abrasive material, ensuring the stability of the sandblasting process. The valve cores and seats frequently contact the abrasives and are thus made of wear-resistant alloys or ceramic materials.
4. Rotary Cages
- Rotary cages are crucial components for evenly distributing abrasives in the sandblasting machine. They continuously rotate during operation, enduring extensive abrasion from the abrasives, and thus require highly wear-resistant materials such as high manganese steel or wear-resistant alloys.
5. Feeders
- Feeders are responsible for evenly delivering abrasives to the nozzles. Their internal structures need wear-resistant materials to cope with continuous abrasive friction. Common materials include wear-resistant steel and hardened alloys.
6. Blast Room Liners
- The inner walls of the blast room are often impacted by high-speed abrasives and need wear-resistant liners for protection. These liners are typically made of high chromium cast iron or steel plates covered with rubber to extend their service life.
7. Rollers
- Rollers are used to transport workpieces in and out of the blast room. These rollers must have high wear resistance to withstand friction from the workpieces and abrasives. Common materials include wear-resistant steel and polyurethane-covered steel rollers.
8. Dust Collectors
- Dust collectors are responsible for removing the dust generated during the sandblasting process, ensuring a clean working environment. The internal filter elements and ducts of the system need a certain level of wear resistance to handle the impact of dust particles. Materials usually include wear-resistant steel and high-strength plastics.
9. Reclamation System
- The reclamation system recovers and cleans used abrasives for reuse. Components such as conveyor belts, screw conveyors, and mixers in this system require wear-resistant materials to extend their service life. Common materials include wear-resistant alloys and high-strength polyurethane.
10. Drums
- Drums are used for batch processing of small workpieces. The inner walls of the drums frequently come into contact with both abrasives and workpieces, requiring highly wear-resistant materials for protection. Common materials include wear-resistant steel and wear-resistant rubber liners.
Conclusion
Choosing the appropriate materials and designs, along with suitable surface treatments, is key to ensuring the wear resistance and service life of sandblasting machine parts. High-quality components such as nozzles, separators, abrasive valves, rotary cages, feeders, blast room liners, rollers, dust collectors, reclamation systems, and drums can significantly enhance the performance and efficiency of sandblasting machines, meeting the needs of various industrial applications. The application of shot peening techniques can further enhance the surface quality and performance of the parts, resulting in higher industrial standards and production efficiency.
Contact Us
Qiao Fu Shen is committed to providing you with products that exceed the industry standards in casting. Our high-quality molds are made from various materials, such as wood, plastic, polystyrene, or metal, depending on your needs. Furthermore, we take pride in offering a wide range of casting sizes and patterns.
We serve numerous industries both domestically and internationally, including but not limited to mechanical hardware parts, tooling machine parts, aerospace components, bicycle parts, and automotive parts. Whether you are looking for specific items or have general inquiries, Qiao Fu Shen 's experienced team is always ready to assist you. We are proud to be one of the most trusted casting companies.
We look forward to speaking with you! Simply fill out the straightforward form below, and our knowledgeable consultants will contact you soon.