How to Mass Produce Sandblasting Machine Components
Using a molding machine to create sand molds and then injecting molten metal into the molds to form the desired shapes of the components, a sandblasting machine is a device used for cleaning and abrasive blasting of surfaces of castings. It requires components that can withstand temperature, pressure, and high-speed operation, such as nozzles, valves, blades, liners, distributors, and control cages.
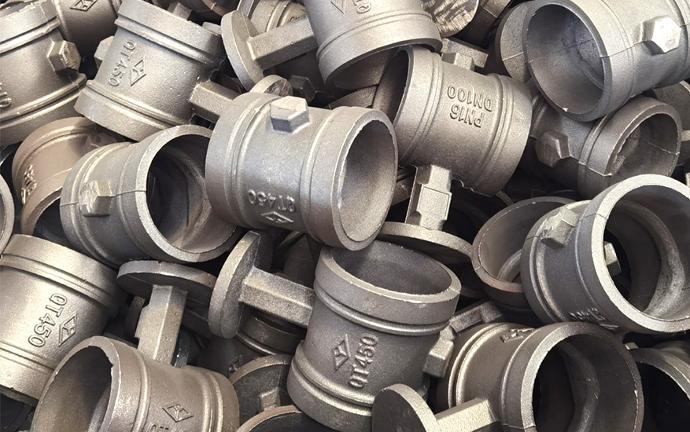
The process of producing sandblasting machine components is as follows
Step 1
Select the appropriate alloy material based on the functionality and specifications of the sandblasting machine parts. The choice of different alloy materials will affect the performance and cost of the components, so it needs to be determined based on market demand and competitiveness.
Step 2
Properly configure alloy raw materials and separately introduce the ingredients into the melting furnace. Heat and melt the alloy raw materials to the required casting temperature. Before pouring, confirm the composition through pre-furnace analysis and ensure the cleanliness and fluidity of the iron melt through degassing and slag removal operations.
Step 3
When the iron melt reaches the casting temperature, inject it into the sand mold cavity, and quickly cool and solidify to form the shape and dimensions of the components. The sand mold should have a well-designed gating system to avoid casting defects such as porosity, sand holes, slag holes, shrinkage, and misruns.
Step 4
Disassemble the cooled and solidified sand mold, remove the casting components, and eliminate excess burrs, flashes, and gating systems. This step requires the use of cutting, grinding, and other tools and equipment to improve the appearance quality and accuracy of the parts.
Step 5
Perform post-treatment on the metal parts, such as heat treatment, surface treatment, and machining, to enhance the strength, wear resistance, and accuracy of the components. The method and extent of post-treatment will be determined based on the usage environment and requirements of the components, such as whether corrosion resistance, rust prevention, and wear resistance are needed.
Step 6
Conduct quality inspection of the casting components, such as dimension measurement, hardness testing, tensile testing, etc., to ensure that the parts meet the requirements for use in sandblasting machines. The methods and standards of quality inspection will be determined based on customer requirements and specifications, such as whether they need to comply with international or domestic certifications.
Methods to Ensure the Quality of Sandblasting Machine Components
Sandblasting machine components are crucial products in a foundry, and they need to possess temperature resistance, pressure resistance, and high-speed operation capabilities to adapt to the working environment of sandblasting machines. To ensure the quality and lifespan of sandblasting machine components, foundries need to control several aspects:
Material selection
Choose suitable alloy materials, such as high-chromium cast iron, high-speed steel, etc., based on the functionality and specifications of sandblasting machine parts. The choice of alloy materials will affect the performance and cost of the components, so it needs to be determined based on market demand and competitiveness.
Mold design
Design a rational mold structure and molding method to meet the shape and size requirements of sandblasting machine components. Mold design affects the flow, filling, and defect generation of molten iron, so it needs to be based on the complexity and precision of the components.
Casting parameters
Use appropriate melting temperature, degassing and slag removal of molten iron, casting speed, and time to ensure that molten iron can quickly and evenly fill the sand mold cavity and solidify rapidly.
Post-treatment methods
Choose suitable post-treatment methods, such as heat treatment, surface treatment, machining, etc., to improve the strength, wear resistance, and accuracy of the components. The choice of post-treatment methods will affect the performance and appearance of the components, so it needs to be based on the usage environment and requirements.
Quality inspection methods
Choose appropriate quality inspection methods, such as visual inspection, dimension measurement, hardness testing, tensile testing, etc., to ensure that components meet the requirements for use in sandblasting machines. The methods of quality inspection will affect the pass rate of components and customer trust, so it needs to be based on customer requirements and specifications.
Contact Us
Qiao Fu Shen is committed to providing you with products that exceed the industry standards in casting. Our high-quality molds are made from various materials, such as wood, plastic, polystyrene, or metal, depending on your needs. Furthermore, we take pride in offering a wide range of casting sizes and patterns.
We serve numerous industries both domestically and internationally, including but not limited to mechanical hardware parts, tooling machine parts, aerospace components, bicycle parts, and automotive parts. Whether you are looking for specific items or have general inquiries, Qiao Fu Shen 's experienced team is always ready to assist you. We are proud to be one of the most trusted casting companies.
We look forward to speaking with you! Simply fill out the straightforward form below, and our knowledgeable consultants will contact you soon.